Projektinformation
- Branche(n): Stahl
Schaffung einer alternativen Verwendung einer auf DRI-Basis erzeugten Elektroofenschlacke für die Zementindustrie zur Verringerung der CO2-Emissionen
- weiterführende Information:
https://www.fona.de/de/massnahmen/foerdermassnahmen/KlimPro/save_co2.php
- Projektlaufzeit: 01.05.2021 - 31.08.2025
- Förderkennzeichen: 01LJ2004
- Fördervolumen des Bundes: ca. 1,7 Mio. €
Kontakt
- Kontakt: David Algermissen
- FEhS – Institut für Baustoff-Forschung e.V.
- Telefon: 02065 9945 12
- E-Mail:
Projektpartner
- FEhS – Institut für Baustoff-Forschung e.V.
Bliersheimer Str. 62, 47229 Duisburg
- Fraunhofer Umwelt-, Sicherheits- und Energietechnik UMSICHT
Osterfelder Straße 3, 46047 Oberhausen
- HeidelbergCement AG
Oberklamweg 2-4, 69181 Leimen
- Thyssenkrupp Steel Europe AG
Kaiser-Wilhelm-Str. 100, 47166 Duisburg
- Universität Duisburg-Essen, Institut für Technologien der Metalle
Forsthausweg 2, 47057 Duisburg
Eisenhüttenschlacken, Nebenprodukte bei der Stahlherstellung, kommen als Sekundärrohstoffe seit Jahrzehnten in Baustoffen zur Anwendung. Dabei werden in großem Umfang CO2-Emissionen vermieden und natürliche Ressourcen geschont. Die schrittweise Transformation der Stahlindustrie hat jedoch radikale Veränderungen bei den Nebenprodukten zur Folge, deren Auswirkungen und Chancen im KlimPro-Industrie Verbundvorhaben SaveCO2 intensiv untersucht werden.
Motivation
Wassergranulierte Hochofenschlacke, der sogenannte Hüttensand, wird in der Zementindustrie gerne als etabliertes Portlandzementklinkersubstitut eingesetzt, da er neben seinen guten Eigenschaften als Bindemittel auch zu einer erheblichen CO2-Reduzierung von knapp fünf Millionen Tonnen jährlich, allein in Deutschland, beiträgt. Dies entspricht zudem einer Rohstoffeinsparung von etwa zwölf Millionen Tonnen pro Jahr.
Durch die Dekarbonisierung in der Stahlindustrie wird dieses Material perspektivisch nicht mehr vorhanden sein, da der Hochofen durch neue Prozesse, wie der Direktreduktionsanlage und dem Elektroniederschachtofen (SAF), ersetzt werden soll. Dadurch entsteht prozessbedingt eine andere Art von Schlacke, die sich ohne weitere Behandlung nicht als (latent) hydraulisches Bindemittel eignet. Durch den Wegfall dieses Stroffstroms wird es in der Zementindustrie daher zu einem deutlichen Anstieg der CO2-Emissionen kommen und gleichzeitig in der Stahlindustrie ein etablierter Absatzpfad der Schlacke entfallen.
Ziele und Vorgehen
Das Projekt SAVE CO2 (Schaffung einer alternativen Verwendung einer auf DRI-Basis erzeugten Elektroofenschlacke für die Zementindustrie zur Verringerung der CO2-Emissionen) widmet sich dieser „neuen" Schlacke und erforscht die Möglichkeit, ein ähnliches Bindemittel aus den sogenannten SAF Schlacken zu erzeugen. Dies soll auch weiterhin der Zementindustrie als Portlandzementklinkersubstitut zur Verfügung stehen, um so auch zukünftig die CO2-Emissionen deutlich zu reduzieren und beide Industrien weiterhin im Sinne der Kreislaufwirtschaft und Ressourcenschonung zu verbinden.
SAVE CO2 erweitert somit die betrachtete Systemgrenze auch über die Stahlindustrie hinaus. So soll ein CO2-Benefit für die deutsche Industrie gesamtheitlich erwirkt werden, was ein weltweites Vorbild für die dekarbonisierte Stahlindustrie mittels Direktreduktionsanlage und SAF sein kann.
Zur Umsetzung dieser Ziele werden im Vorhaben unterschiedliche Qualitäten von direkt reduziertem Eisen aufgeschmolzen und die entstehende Schlacke untersucht. Basierend auf den so gewonnenen Erkenntnissen werden in umfangreichen Labor- und Technikumsversuchen Konzepte entwickelt und erprobt, wie eine zukünftige Konditionierung der Schlacken funktionieren kann. Vielversprechende Konzepte werden anschließend in einem speziell für das Vorhaben angefertigten Elektroofen im größeren Maßstab umgesetzt, um die erforderlichen zement- und betontechnischen Untersuchungen durchführen zu können. Spezialisten für Ökobilanzierungen begleiten das gesamte Vorhaben, um eine fundierte Aussage über die umwelttechnischen Aspekte des entwickelten Verfahrens tätigen zu können.
Partner und Verwertung
Das Vorhaben wird koordiniert vom FEhS – Institut für Baustoff-Forschung e.V., das auf die gesammelte Expertise aus 70 Jahren Forschung im Bereich der Eisenhüttenschlacken zurückgreifen kann. Der Lehrstuhl für Metallurgie der Eisen- und Stahlerzeugung der Universität Duisburg-Essen betrachtet insbesondere die metallische Phase und ist für die Durchführung der Schmelzversuche mit DRI in einem speziell für das Vorhaben entwickelten Elektroofen verantwortlich. Die ökologische und ökonomische Begleitung des Vorhabens wird von den Spezialisten des Fraunhofer UMSICHT durchgeführt. Als Industriepartner sind Deutschlands größter Stahlerzeuger, thyssenkrupp Steel Europe und der zweitgrößte Zementerzeuger weltweit, HeidelbergCement, integraler Bestandteil des Konsortiums. Durch diesen interdisziplinären Verbund von Partner aus unterschiedlichen Industrien und wissenschaftlichen Bereichen können alle technischen, ökonomischen und ökologischen Aspekte des Vorhabens fundiert betrachtet werden und, so die Ambitionen der Partner, zum gegenseitigen Vorteil der gesamten deutschen Stahl- und Zementindustrie umgesetzt werden.
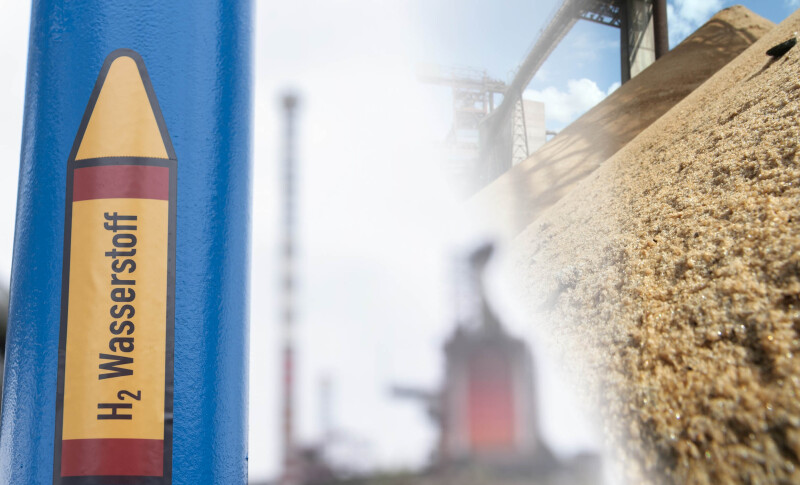
Vom Wasserstoff zum Hüttensand © FEhS - Institut für Baustoff-Forschung e.V. / thyssenkrupp Steel Europe AG

Wassergranulation im Schmelzlabor des FEhS © FEhS - Institut für Baustoff-Forschung e.V.