Projektinformation
- Branche(n): Stahl
Nutzung von CO2 im Heißwind zur Effizienzsteigerung im Hochofen
- Projektlaufzeit: 01.08.2022 - 31.12.2025
- Förderkennzeichen: 01LJ2108A
- Fördervolumen des Bundes: 985.792 €
Kontakt
- Kontakt: Rüdiger Deike
- Universität Duisburg-Essen, Institut für Technologien der Metalle
- Telefon: 0203 379 3455
- E-Mail:
Projektpartner
- Technische Universität Clausthal, Institut für Metallurgie (TUC, IMET)
Robert-Koch-Str. 42, 38678 Clausthal-Zellerfeld
- thyssenkrupp Steel Europe AG (tkSE)
Kaiser-Wilhelm-Str. 100, 47166 Duisburg
- Universität Duisburg-Essen, Institut für Technologien der Metalle (UDE, ITM)
Friedrich-Ebert-Str. 12, 47119 Duisburg
CO2-Emissionen entstehen während der Roheisenherstellung auf der herkömmlichen Hochofenroute prozessbedingt. Aus diesem Grund setzt die Stahlindustrie zukünftig auf eine alternative Prozessroute, welche die CO2-Emissionen minimiert. Jedoch benötigt die Umrüstung der Prozesstechnologie Zeit, sodass die alternative Prozessroute erst in vielen Jahren vollständig etabliert sein wird. Für die Übergangszeit ist es notwendig ein Konzept zu entwickeln, das entstehendes CO2 möglichst sinnvoll nutzt und damit die Emissionen schon bis 2030 reduziert.
Interview mit Lucas Horn vom 08. April 2025 zum Projekt NuCOWin
Vor seiner Amtsübergabe hat das ReInvent-Team ein schriftliches Interview mit Lucas Horn, dem ehemaligen Projektleiter von NuCOWin, geführt, um mehr über die Projektergebnisse und die Ambitionen zur Fortführung und Verfestigung der entwickelten Innovationen zu erfahren. Lesen Sie hier das Interview oder scrollen Sie zunächst weiter und erfahren Sie mehr über die Grundlagen und die Motivation zum Projekt.
Motivation
Die großen Stahlunternehmen planen in den kommenden Jahrzenten die Hochofenroute zur Roheisenherstellung durch alternative Prozessrouten zu substituieren. Von zentraler Bedeutung sind hierbei Direktreduktionsanlagen in Kombination mit elektrischen Einschmelzaggregaten, welche an die Stelle der konventionellen Hochöfen treten sollen. Direktreduktionsanlagen arbeiten mit Reduktionsgasen, welche bei Überdruck und hohen Temperaturen Sauerstoff aus dem Eisenerz separieren und dieses somit zu Eisen reduzieren. Bei genanntem Prozess wird das entstehende Eisen nicht verflüssigt, weshalb ein anschließendes Einschmelzen mittels elektrischer Energie notwendig wird. Als Reduktionsgas soll zukünftig Wasserstoff eingesetzt und elektrische Energie aus regenerativen Quellen bezogen werden. Allerdings wird es noch Jahrzehnte dauern, bis eine entsprechende Infrastruktur für die regenerative Strom- und Wasserstofferzeugung geschaffen ist. Aus diesem Grund sollen Direktreduktionsanlagen in einer Übergangsphase zunächst mit Erdgas betrieben werden. Als Kuppelprodukt entsteht hierbei hochreines CO2, welches in den Hochöfen wiederverwertet werden soll, da es in den nächsten 20 bis 30 Jahren einen Parallelbetrieb der konventionellen Hochöfen und der modernen Direktreduktionsanlagen geben wird.
Ziele und Vorgehen
Das Projekt NuCOWin (Nutzung von CO2 im Heißwind zur Effizienzsteigerung im Hochofen) widmet sich dieser Wiederverwertung und erforscht den Einsatz von CO2 im Heißwind. Die Grundidee des Projekts zeichnet sich durch die systemische Betrachtung von Direktreduktionsanlagen und Hochöfen als temporär koexistierende Einheiten aus. So soll im Direktreduktionsprozess anfallendes CO2 als Kohlenstoff und Sauerstoffträger nutzbringend im Hochofen eingesetzt werden, um über den gesamten Hüttenverbund CO2-Emissionen zu verringern. Durch das Einbringen von CO2 in den Hochofen wird darüber hinaus Luft, welche zu einem Großteil aus dem Inertgas Stickstoff besteht, substituiert. Dies hat zur Folge, dass sich die Gichtgaszusammensetzung grundlegend verändert. Als Konsequenz wird ein höherwertiges Gichtgas erwartet, das den nachgeschalteten Prozessen eines integrierten Hüttenwerkes zugeführt und unter Umständen sogar erneut als Reduktionsgas in einer
Direktreduktionsanlage eingesetzt werden kann. Basierend auf dieser Idee sollen Erkenntnisse in umfangreichen Labor- und Technikumsversuchen gewonnen und Konzepte zum nutzbringenden CO2-Recycling sowohl entwickelt als auch erprobt werden. Da die im Hochofen ablaufenden Prozesse aufgrund der Gleichzeitigkeit von exotherm und endotherm ablaufenden irreversiblen Reaktionen hochgradig komplex sind, muss zudem eine detaillierte Modellbildung und Prozesssimulation erfolgen.
Partner und Verwertung
Das Vorhaben wird vom Lehrstuhl für Metallurgie und Umformtechnik der Universität Duisburg-Essen koordiniert. Zudem erfolgen die Modellbildung und Prozesssimulation in Duisburg. Das Institut für Metallurgie der Universität Clausthal beschäftigt sich vor allem mit der praktischen Versuchsdurchführung und ist für die Entwicklung des Versuchsstandes und die Durchführung der Versuche zuständig, anhand derer die Prozesssimulation validiert werden kann. Zudem ist Deutschlands größter Stahlerzeuger, die thyssenkrupp Steel Europe AG, ein wichtiger Industriepartner des Konsortiums. Durch den Verbund von interdisziplinär agierenden Partnern sollen alle technischen, ökonomischen und ökologischen Fragestellungen des Vorhabens fundiert betrachtet und gelöst werden, um die Ambitionen der Partner zum gegenseitigen Nutzen, zum Vorteil der gesamten deutschen Stahlindustrie und des Umweltschutzes umzusetzen.
Interview mit Lucas Horn vom 08. April 2025 zum Projekt NuCOWin
Vor seiner Amtsübergabe hat das ReInvent-Team ein schriftliches Interview mit Lucas Horn, dem ehemaligen Projektleiter von NuCOWin, geführt, um mehr über die Projektergebnisse und die Ambitionen zur Fortführung und Verfestigung der entwickelten Innovationen zu erfahren. Lesen Sie hier das Interview.
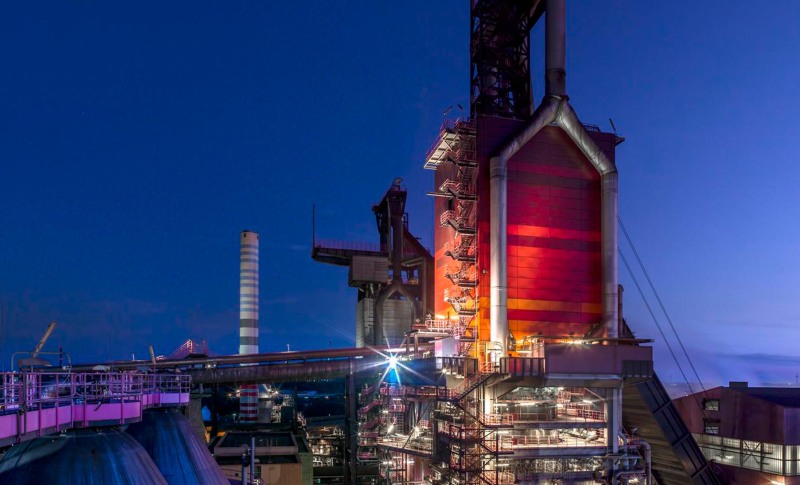
Hochöfen Hamborn der thyssenkrupp Steel Europe AG © thyssenkrupp Steel Europe AG
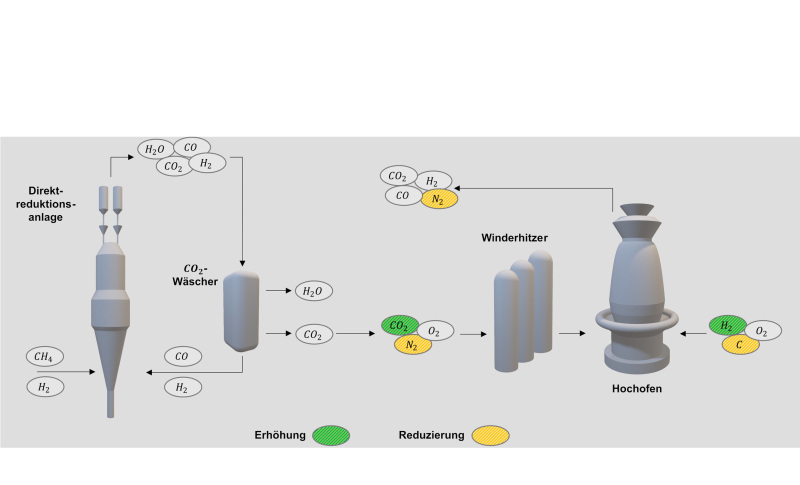
Kopplung von Direktreduktionsanlage und Hochofen in einem integrierten Hüttenwerk © Universität Duisburg-Essen, ITM