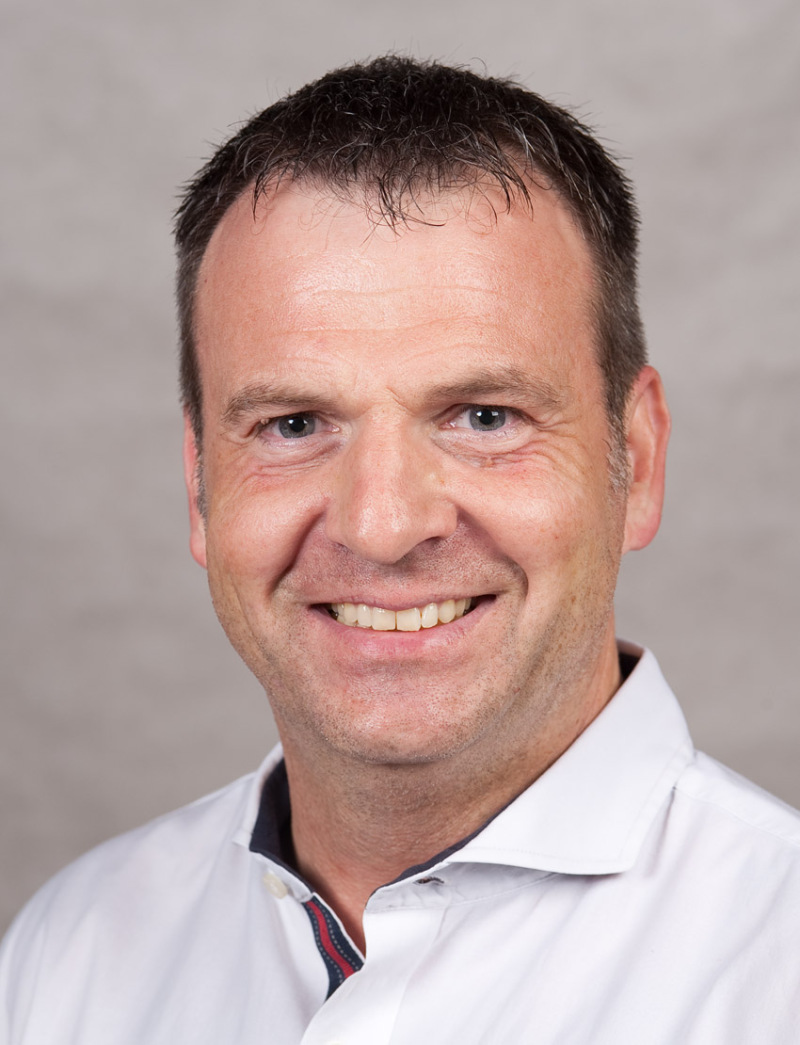
Dr. Dirk Schmitt, Heidelberg Materials AG
Sehr geehrter Dr. Schmitt, in der konventionellen Herstellung von Zement werden große Mengen CO2 durch die Herstellung des Zementklinkers freigesetzt. Zementklinker ist heutzutage ein wesentlicher Bestandteil, der für die Erhärtung des Zements notwendig ist. Im KlimPro-Industrie-Verbundforschungsvorhaben „K4 - Kohlendioxidreduktion durch kalkarme Klinker und Karbonatisierungshärtung“, welches Sie koordinieren, wird belitischer Klinker unter Verwendung des Recyclingmaterials „hydratisierter, erhärteter Zementstein“ aus Abbruchbeton (RCP, Recycled Concrete Paste) entwickelt. Was sind die Vorteile und Herausforderungen?
Rezyklierter Zementstein, sogenanntes RCP, ist ein bisher ungenutztes Nebenprodukt des Betonrecyclings. Die Verwendung von RCP in der Klinkerherstellung bietet zwei interessante Möglichkeiten:
Einerseits liefert das Material eine CO2-freie Calciumquelle, andererseits kann die erforderliche Brenntemperatur bei der Herstellung von K4-Klinker reduziert werden, so dass weniger Brennstoffe eingesetzt werden müssen. Diese Effekte eröffnen die Möglichkeit, CO2-Emissionen in der Klinkerherstellung zu vermeiden.
Wir schätzen RCP aber nicht nur wegen seiner herausragenden Eigenschaften, sondern auch, um die Kreislaufwirtschaft in der Zement- und Betonindustrie voranzutreiben. Dadurch können wertvolle Primärrohstoffe geschont und Bau- sowie Abbruchmaterialien wertschöpfend verwendet werden.
Um RCP jedoch für die Herstellung von K4-Klinker einsetzen zu können, muss es einen hohen Calciumgehalt haben. Mit den derzeit verwendeten Abbruch- und Recyclingmethoden wird üblicherweise eine so hohe Qualität nicht erreicht. Dank des von Heidelberg Materials entwickelten und bereits in Deutschland und Polen erprobten selektiven Betonrecyclingverfahrens ist dies erstmals im industriellen Maßstab möglich.
In K4 wird die permanente Bindung von CO2 durch sogenannte Karbonatisierungshärtung der aus RCP hergestellten Zemente untersucht. Wie grenzt sich die im Rahmen von K4 angestrebte Karbonatisierungshärtung von anderen Verfahren zur Beaufschlagung von Beton mit CO2 ab?
Im Rahmen von K4 untersuchen die Projektpartner den Prozess der Karbonatisierungshärtung. Bei diesem Prozess werden die grünstandfesten Betonelemente direkt nach der Verdichtung in speziell entwickelten Nachbehandlungskammern einer CO2-haltigen Atmosphäre ausgesetzt. Während dieser Aushärtung dominiert die spontan ablaufende Karbonatisierungsreaktion die Hydratation, die für die Aushärtung von traditionellem Beton verantwortlich ist.
K4 nutzt diesen Vorteil: Die Karbonatisierung aktiviert die Reaktivität von belitischem Klinker, um eine erhebliche Menge CO2 dauerhaft im Beton einzubinden und leistungsfähige Betonprodukte herzustellen. Dadurch kann K4-Zement für moderne, nachhaltige Betonprodukte eingesetzt werden, die aufgrund ihrer hohen Leistungsfähigkeit den hohen Anforderungen des Marktes gerecht werden.
Im Projekt sollen CO2-Härtekammern so konzipiert werden, dass Temperatur, Feuchte und CO2-Konzentration eine optimale Karbonatisierungshärtung von Betonprodukten gewährleisten. Können Sie uns bereits einen Einblick dazu geben, wie die o.g. Parameter hierzu idealerweise gewählt werden sollten?
Die industrielle Entwicklung begleiten wir im Rahmen des Projekts durch wissenschaftliche Studien, die sich darauf konzentrieren, die ablaufenden Reaktionsmechanismen zu identifizieren und zu verstehen.
Dies ermöglicht uns, die entscheidenden Einflussfaktoren für eine gute CO2-Durchdringung des Betonelements und eine optimal ablaufende Reaktion zu identifizieren. Basierend auf diesen Erkenntnissen können wir die einzelnen Phasen des Härtungsprozesses optimieren und die gewünschte Produktleistungsfähigkeit gezielt steuern.
Wir wollen noch nicht zu viel verraten: Aber wir sind in der Lage den Prozess effizient bei Atmosphärendruck, also ohne Verwendung von Überdruck, zu steuern und benötigen dafür kein aufwändig gereinigtes hochkonzentriertes CO2, sondern können direkt die Ofenabgase der Klinkerherstellung als CO2-Quelle nutzen.
Wie hoch wird nach Ihrer Ansicht das Potenzial für eine industrielle Anwendung der Forschungsergebnisse sein?
Für eine erfolgreiche industrielle Anwendung gibt es verschiedene Erfolgsfaktoren. Ein ausschlaggebender Faktor ist die Verfügbarkeit der benötigten Rohstoffe RCP und CO2. Durch die in den letzten Jahren intensiven Entwicklungsaktivitäten in diesen Bereichen und bereits vorhandene Expertise in der großtechnischen Umsetzung kann Heidelberg Materials dies sicherstellen.
Ergänzend dazu hat Kraft Curing Systems im Rahmen des Projekts gezeigt, wie viel Expertise für die kontrollierte Steuerung von Nachbehandlungskammern erforderlich ist, um hohe CO2-Konzentrationen sicher zu betreiben.
Aber natürlich geht es am Ende um das Produkt, dessen Leistungsfähigkeit stimmen muss. Im Rahmen von K4 konnten die Projektpartner in den durchgeführten Laborversuchen und bei Lithonplus durchgeführten Feldversuchen das hohe Potenzial von karbonatisierungsgehärtetem Beton aufzeigen. Die Technologie ist ideal, um den Markt mit leistungsfähigen Betonprodukten, die CO2 dauerhaft einbinden und die Kreislaufwirtschaft fördern zu bereichern.
Basierend auf all diesen Erkenntnissen steht einer industriellen Anwendung nichts im Wege.
Herzlichen Dank für die Beantwortung der Fragen! Wir wünschen Ihnen weiterhin viele Erfolge im Projekt!
Das Interview wurde am 17. Dezember 2024 schriftlich mit Herr Dr. Dirk Schmitt geführt und mit dessen Einverständnis am 14. Januar 2025 veröffentlicht.